Abstract
Under the condition of extremely high safety requirements, the Non-Intrusive Ultrasonic Level Gauge can accurately measure without opening the tank or drilling the tank, and only need to attach the probe to the external surface of the tank bottom, with a measurement accuracy of 1%, and will not be affected by pressure, medium or even temperature.
Overview of Horizontal Tank
Horizontal tanks are long containers for the storage of crude oil, vegetable oils, chemical solvents, LPG, water, or other petroleum products. Horizontal tank is composed of end cover and horizontal round or oval tank wall and saddle. The volume of the horizontal tank is generally less than 100 cubic meters, it is generally round, oval, there are other irregular shapes.
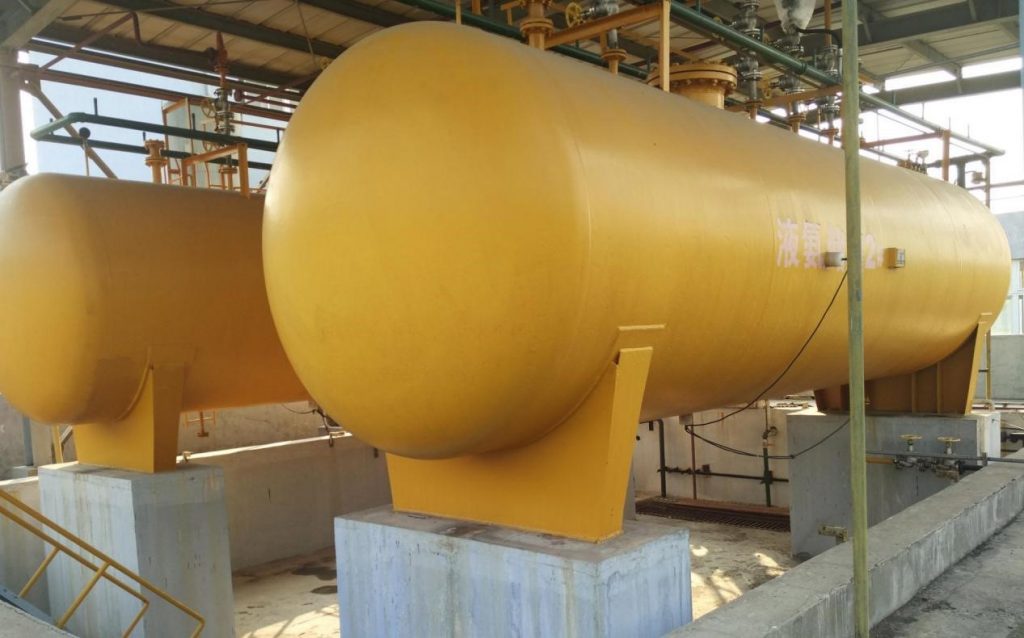
Characteristics of the Horizontal Tank
- The medium in the horizontal tank: Liquid ammonia, liquefied gas, propylene, propane, liquid chlorine, hydrogen fluoride, bromine, ethylene oxide, monomer, hydrogen chloride, nitric acid, gasoline, diesel, aviation kerosene, tertiary butylamine, sulfur dioxide.
- Safety requirements: first class explosion-proof
- Pressure: 0.1 to 1.3mPa
- Temperature :-20℃ to -32℃
- Horizontal tank material: carbon steel, aluminum can, stainless steel, lined with enamel carbon steel tank
- Wall thickness: 10 mm to 20 mm
- Diameter: 1000 mm – 6000 mm
Difficulties in measuring Horizontal Tank:
- Safety factor: because the Horizontal tank is a pressure tank, the hole cannot be opened in the production process, and contact level meters such as radar level meter and float ball level meter cannot be replaced normally after damage, so production needs to stop and shutdown. Meanwhile, the liquid in the storage tank needs to be emptied, which is difficult to install and high risk coefficient.
- Speed of liquid in and out: the faster the speed of liquid in, the greater the impact on the lower liquid level, the more difficult to measure, so the normal installation should be more than 1 meter away from the inlet to prevent the impact of large liquid in the measurement.At the same time, the liquid intake mode will also interfere with the measurement, and the production liquid intake is relatively stable, but the external procurement liquid intake is the piston pump liquid intake, the liquid intake instability will cause a big impact on the level measurement.
- Precipitation thickness: the greater the influence of precipitation thickness on the thickness, the greater the gain, the larger the blind area, the unstable echo, etc., will have a great impact on the measurement, when the precipitation is too thick.
- Viscosity coefficient: generally, the dynamic viscosity of the tested medium is required to be less than 10 mPa.S.When 10 mPa.S < dynamic viscosity < 30 mPa.S, the instrument range may be reduced and the blind area will be increased.The dynamic viscosity > 30 mPa.S cannot be measured.(1 mPa.S = 1 cP)
Solutions:
Non-Intrusive Ultrasonic Level Gauge does not need to be opened in the tank hole, and the pressure, temperature, density, viscosity and media is independent, so the choice of external paste type level meter can be a good solution to the above problems.
Installation of Non-Intrusive Ultrasonic Level Gauge
Probe installation: probe installation position tank wall smooth leaking tank wall, probe close to the tank wall, avoid liquid in and out of the mouth, generally installed in within one meter away from the valve at the bottom of the column, due to keep the probe in a horizontal position, so the probe is placed between the tank wall or a film base, make its level (also can be installed in the valve bar).The calibration probe is mounted at the equator of the spherical tank. Not close to the weld.
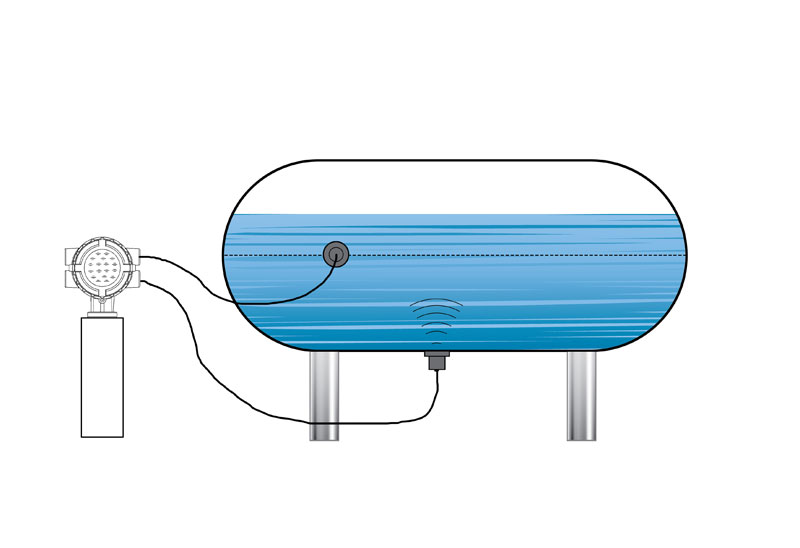
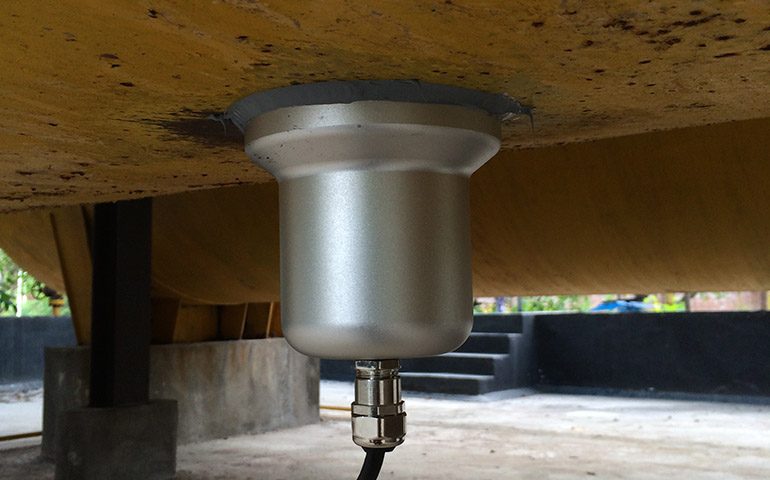
Instrument debugging: to know the height of tank, the diameter, medium, temperature, and the actual height of liquid level, into the user parameter input height of tank, the default speed of sound (1000), the migration amount (probe installation position and other liquid level meter zero gap, the probe position 100 mm 100 vice plus 100), the waveform interface using the remote control according to the six consecutive 1 set correct frequency (80-400) under the blind area is smaller, the smaller the gain, frequency, the best in finding the best frequency, set up the correct sound velocity, envelope degrees (the larger the range, the greater the envelope smooth waveform).When there is a side calibration probe, it is necessary to enter the menu to set the correct diameter of the side and the height of the side calibration probe, change the measurement mode to the calibration mode, and then enter the waveform interface, change M (measurement) to C (calibration), adjust the correct frequency with the above method, change C (0) to C (1) to start the calibration.No more than half of the liquid level was used with a single probe.
Perfect connection with DCS or SIS
Non-Intrusive Ultrasonic Level GaugeBecause is a two-wire system design, it can be connected with the factory’s DCS system or SIS system. DCS system mainly displays and tracks the liquid level, while SIS system mainly controls the valve for the interlock system.